Projekty Lean
Optymalizacja magazynu: klucz do skuteczności w branży meblarskiej
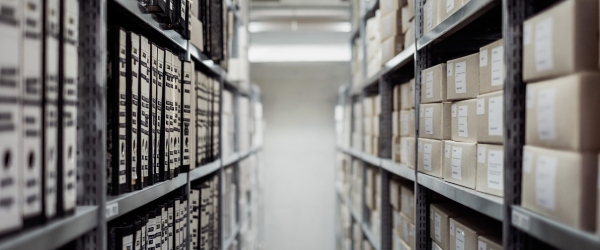
W dynamicznym świecie przemysłu meblarskiego, skuteczne zarządzanie magazynem stanowi kluczowy czynnik wpływający na konkurencyjność i efektywność operacyjną firmy. Poniżej opisujemy jeden z najciekawszych business case z jakim mieliśmy do czynienia w ostatnim czasie.
Zostaliśmy zaproszeni do współpracy przez z jednego czołowych producentów mebli w Polsce, w celu przeprowadzenia kompleksowej analizy procesów realizowanych w obrębie magazynu surowców oraz obszaru kompletacji wydań na produkcji. Jak cel nadrzędny, postawiono nam podniesienie efektywności pracy na magazynie.
Zgodnie z wybudowaną wieloletnią praktyką, nasze działania rozpoczęły się od kompleksowej analizy wskazanych obszarów, w celu doboru optymalnej metody oceny efektywności realizowanych procesów. Należy tu zaznaczyć ze mieliśmy szczęście w postaci klienta który rozumie że skuteczne działania wymagają odpowiednio przygotowanego gruntu a tym była dla nas faza analizy problemu. Dopiero skuteczne przeprowadzenie tej części projektu gwarantuje prawidłowe i trwałe wdrażanie proponowanych działań korygujących.
Analiza:
Na wstępnym etapie prac zdecydowaliśmy się oprzeć nasze działania na metody MTM a dokładniej jej metodyki stosowanej w Logistyce. Pozwoliło nam to na właściwe zbudowanie modelu aktualnej pracy i jednocześnie zamodelowanie efektywności pracy pracowników w modelu docelowym w kilku wariantach – zgodnie z oczekiwaniami klienta.
Praca została szybko podzielona na 2 główne obszary: proces przyjęć towarów oraz magazynowania i kompletacji wydań.
I. Przyjęcia towarów
Diagnoza:
Po zakończonym etapie analizy w obszarze przyjęć towarów, jako niektóre z głównych problemów wskazane zostały:
Ponadto, bazując na narzędziach jakie oferuje na MTM, efektywność pracy została skalkulowana na poziomie 48%, średnio dla 4 pracowników na zmianę, w podobszarach odbioru dostaw paletowych i obszarach pozostałych. Co warte podkreślenia, na etapie obserwacji zidentyfikowano około 15% ogólnej nieefektywności w procesach (co jest mimo wszystko naturalnym zjawiskiem) które zostały wkalkulowane w wynik końcowy.
Terapia:
Oczywiście na tym etapie rodzi się pytanie co zostało wykonanie i jakie przyniosło to działania końcowe.
Jedną z głównych rekomendacji jakie zostały zaproponowane były:
Efekty:
Wdrożenie rekomendacji opisanych powyżej pozwoliło finalnie na podniesienie średniej efektywności pracy magazynierów do około 65% przy jednoczesnym zmniejszeniu liczby pracowników w obszarze z 4 do 3 osób na zmianę. Ponadto, wypoziomowanie procesów dostawy pozwoliło na stabilniejszą pracę w kolejnych obszarach pracy magazynu bez konieczności „szarpania” całym systemem pracy i pilnym delegowaniem dodatkowych osób z pozostałych obszarów magazynu w sytuacji skumulowania kilku dostaw w tym samym czasie.
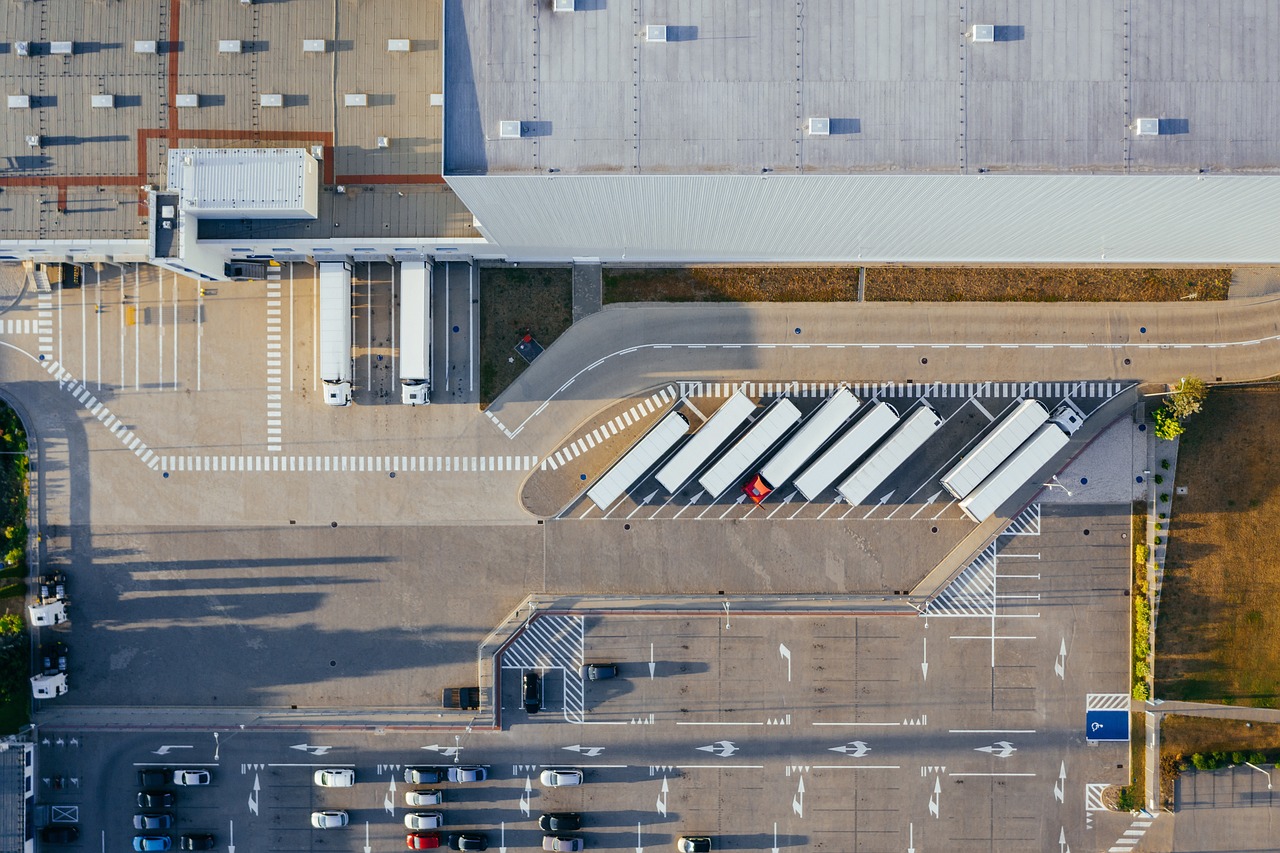
II. Magazynowania i kompletacji wydań.
Analiza:
Obszar ten stanowił większe wyzwanie z uwagi na liczbę dziennych kompletacji, obszar obserwacji oraz skalę analizowanych danych systemowych. W obszarze magazynowania i kompletacji jako baza posłużyły nam dane z systemu WMS klienta, w którym zarejestrowane były wszystkie ruchu materiału wewnątrz magazynu i przesunięcia systemowe. „Podłożenie” ich w uprzednio przygotowany model matematyczny zbudowany w oparciu o metodykę MTM, pozwolił nam jednoznacznie ocenić bieżącą efektywność pracowników oraz zamodelować kilka potencjalnych scenariuszy pracy po wdrożeniu zmian w procesie kompletacji, wydawania komponentów na produkcję i procesów powiązanych.
Diagnoza:
Wśród najważniejszych nieefektywności i problemów jakie zidentyfikował nasz zespół kluczowymi były:
Terapia:
Jako priorytetowe działania zarekomendowane i zaakceptowane przez zespół projektowy oraz Komitet Sterujący wdrożone zostały następujące kwestie:
Efekty:
Implementacja wymienionych wyżej inicjatyw oczywiście wymagała szczegółowego zaplanowania i rozłożenia w czasie tak, aby wprowadzane zmiany w jak najmniejszym stopniu zagrażały płynności przebiegu procesów produkcyjnych. Po kilku tygodniach wzmożonych działań, wdrożenie zmian przez zespół projektowy pozwoliło m.in. na:
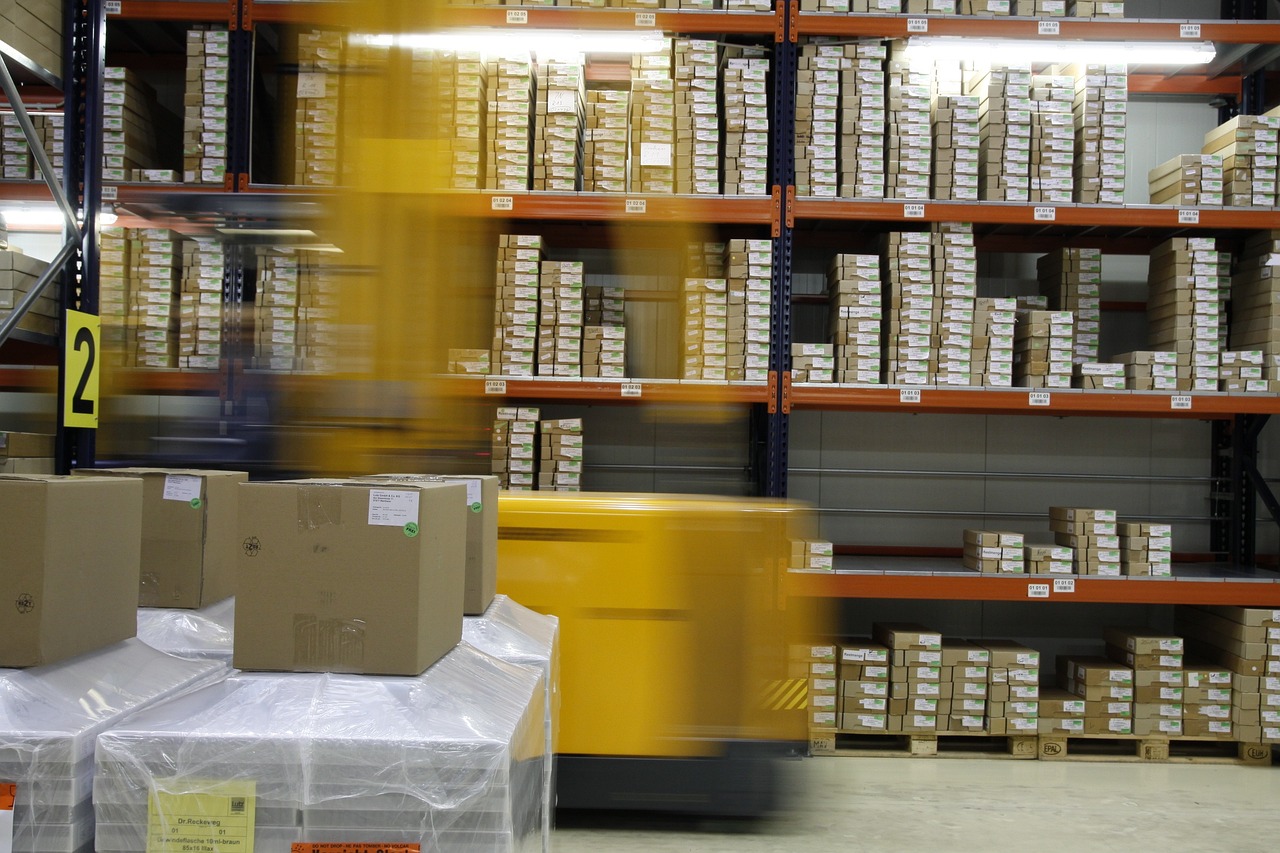
Podsumowanie
Konsekwentne trzymanie się podstaw zasad odchudzonej produkcji i metodyki problem solving (Raport A3 – PDCA) wraz z zastosowanie skutecznych narzędzie jakie niesie ze sobą metodyka normowania MTM, pozwoliła na skuteczne i szybkie wdrożenie zidentyfikowanych potencjałów. Co istotne dla klienta, działania w obszarze magazynu wpłynęły również na pozytywny trend obniżenia części pozycji kosztowych związanych m.in. z wartością magazynu surowca i docelowym obniżeniem kosztów operacyjnych obsługi wózków widłowych. Wdrożenie metodyki pracy podczas kompletacji pozwoliła poprawić średnią efektywności pracowników przy zachowaniu bezpiecznego balansu pracy. Na koniec, sama inwestycja w prace projektowe i wdrożeniowe pozwoliła na osiągnięcie realnego ROI z wprowadzonych zmian w okresie poniżej 12 miesięcy.
Życzymy wszystkim naszym klientom tak dużego zaangażowania w prace projektowe oraz chęci do wprowadzenia zmian w organizacji.
Zgodnie z wybudowaną wieloletnią praktyką, nasze działania rozpoczęły się od kompleksowej analizy wskazanych obszarów, w celu doboru optymalnej metody oceny efektywności realizowanych procesów. Należy tu zaznaczyć ze mieliśmy szczęście w postaci klienta który rozumie że skuteczne działania wymagają odpowiednio przygotowanego gruntu a tym była dla nas faza analizy problemu. Dopiero skuteczne przeprowadzenie tej części projektu gwarantuje prawidłowe i trwałe wdrażanie proponowanych działań korygujących.
Analiza:
Na wstępnym etapie prac zdecydowaliśmy się oprzeć nasze działania na metody MTM a dokładniej jej metodyki stosowanej w Logistyce. Pozwoliło nam to na właściwe zbudowanie modelu aktualnej pracy i jednocześnie zamodelowanie efektywności pracy pracowników w modelu docelowym w kilku wariantach – zgodnie z oczekiwaniami klienta.
Praca została szybko podzielona na 2 główne obszary: proces przyjęć towarów oraz magazynowania i kompletacji wydań.
I. Przyjęcia towarów
Diagnoza:
Po zakończonym etapie analizy w obszarze przyjęć towarów, jako niektóre z głównych problemów wskazane zostały:
- nieregularna praca w zależności od dostawy towaru (MURA)
- ryzyko ergonomiczne – dużo pracy ręcznej, przenoszenie dużych paczek, ryzyko przeciążenia (MURI)
- występowanie zbędnych procesów jak np. ręczne kopiowanie części kodu komponentów markerem na opakowaniu (MUDA)
Ponadto, bazując na narzędziach jakie oferuje na MTM, efektywność pracy została skalkulowana na poziomie 48%, średnio dla 4 pracowników na zmianę, w podobszarach odbioru dostaw paletowych i obszarach pozostałych. Co warte podkreślenia, na etapie obserwacji zidentyfikowano około 15% ogólnej nieefektywności w procesach (co jest mimo wszystko naturalnym zjawiskiem) które zostały wkalkulowane w wynik końcowy.
Terapia:
Oczywiście na tym etapie rodzi się pytanie co zostało wykonanie i jakie przyniosło to działania końcowe.
Jedną z głównych rekomendacji jakie zostały zaproponowane były:
- wdrożenie planowania dostaw przy współpracy z działem transportu i lokalnymi dostawcami w celu możliwości płynnego planowania pracy w obrębie ramp rozładunkowych
- poprawa ergonomii poprzez modyfikacje wózków transportowych w celu umożliwienia dostarczania ich bezpośrednio do ciężarówki – eliminacja konieczności ręcznego transportu paczek
- eliminacja zbędnego procesu – znakowanie opakowania markerem – zastosowano ręczne drukarki atramentowe.
Efekty:
Wdrożenie rekomendacji opisanych powyżej pozwoliło finalnie na podniesienie średniej efektywności pracy magazynierów do około 65% przy jednoczesnym zmniejszeniu liczby pracowników w obszarze z 4 do 3 osób na zmianę. Ponadto, wypoziomowanie procesów dostawy pozwoliło na stabilniejszą pracę w kolejnych obszarach pracy magazynu bez konieczności „szarpania” całym systemem pracy i pilnym delegowaniem dodatkowych osób z pozostałych obszarów magazynu w sytuacji skumulowania kilku dostaw w tym samym czasie.
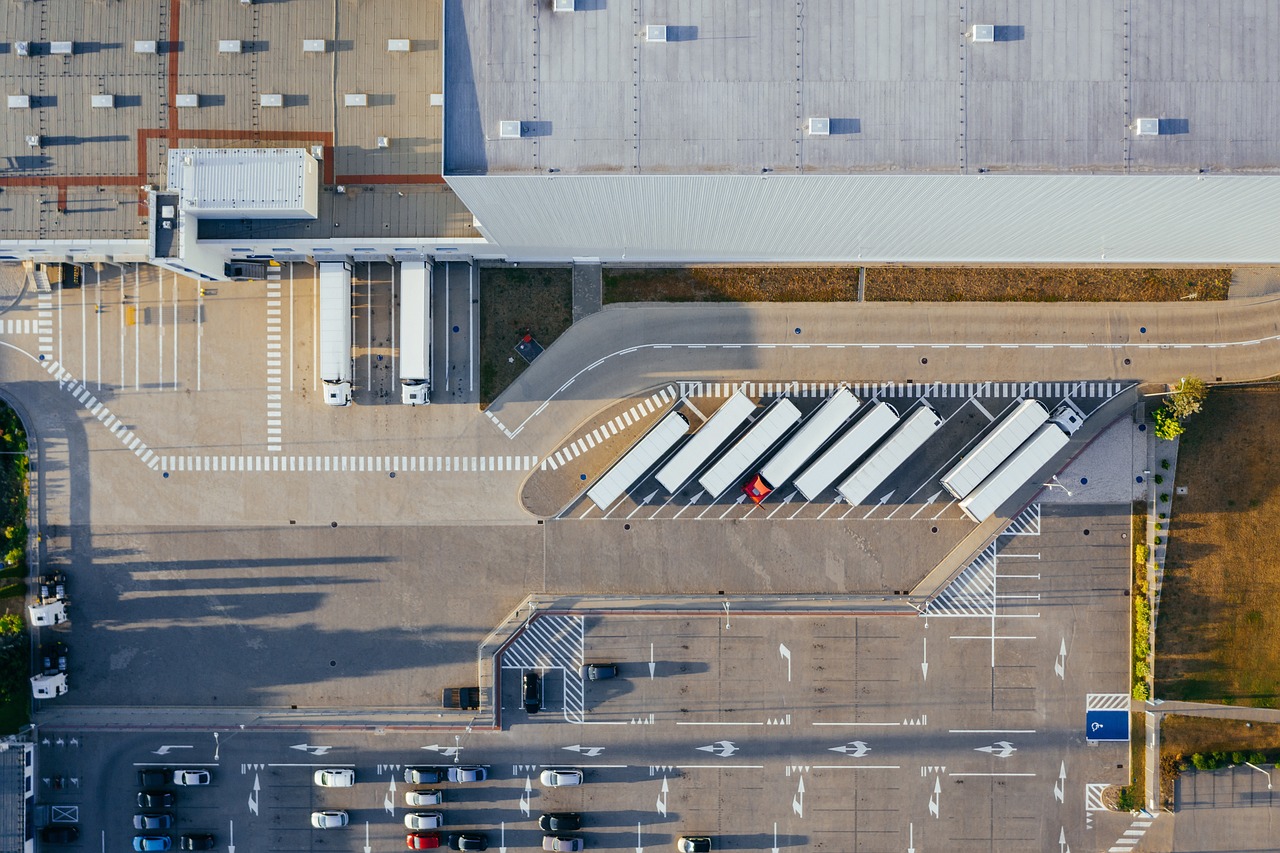
II. Magazynowania i kompletacji wydań.
Analiza:
Obszar ten stanowił większe wyzwanie z uwagi na liczbę dziennych kompletacji, obszar obserwacji oraz skalę analizowanych danych systemowych. W obszarze magazynowania i kompletacji jako baza posłużyły nam dane z systemu WMS klienta, w którym zarejestrowane były wszystkie ruchu materiału wewnątrz magazynu i przesunięcia systemowe. „Podłożenie” ich w uprzednio przygotowany model matematyczny zbudowany w oparciu o metodykę MTM, pozwolił nam jednoznacznie ocenić bieżącą efektywność pracowników oraz zamodelować kilka potencjalnych scenariuszy pracy po wdrożeniu zmian w procesie kompletacji, wydawania komponentów na produkcję i procesów powiązanych.
Diagnoza:
Wśród najważniejszych nieefektywności i problemów jakie zidentyfikował nasz zespół kluczowymi były:
- nieoptymalna metodyka kompletacji zleceń polegająca na kompletacji 1 zlecenia w kilku krokach, generująca powstawanie kilku buforów międzyoperacyjnych
- dodatkowe transporty komponentów pomiędzy obszarami
- układ komponentów na magazynie niedostosowany do bieżącego zapotrzebowania – wymuszone dodatkowe ruchy pracowników i wózków podczas kompletacji
- dostarczanie ok 20% komponentów z magazynków znacznie oddalonych od głównej strefy kompletacji
- Pobieranie ok 50% komponentów wózkiem systemowym (powyżej poziomu kompletacji ręcznej) – co generuje dodatkowe ruchy magazynowe
- Średni czas kompletacji jednego zlecenia wykonywany ok 60% dłużej aniżeli wskazywała by to norma wg kalkulacji metodą MTM
- Obliczona, średnia efektywność pracowników wahała się od ok 30% do 55% w zależności od analizowanego obszaru (w 5-ciu podobszarach magazynowania). Średnia efektywność pracy magazynierów kształtowała się na poziomie ok 44%.
Terapia:
Jako priorytetowe działania zarekomendowane i zaakceptowane przez zespół projektowy oraz Komitet Sterujący wdrożone zostały następujące kwestie:
- zmiana metodyki kompletacji komponentów do wydań na produkcji zgodnie z metodą 1 piece flow, eliminując powstawanie dodatkowych buforów i transportów. W praktyce oznaczało to połączenie 3 dotychczas rozłącznych, stref pracy w magazynie w 1 obszar.
- relokacja komponentów na magazynie z uwzględnieniem bieżącego zapotrzebowania i nowych ścieżek kompletacji (maksymalizacja pobierania z poziomów dostępnych dla magazynierów ) + eliminacja komponentów nierotujących
- wdrożenie standardu dynamicznej weryfikacji optymalnego rozłożenia komponentów
- optymalizacji i redukcja średniej liczby transportów paletowych o 32% – mogących być wykonanym wyłącznie wózkiem magazynowym
- opracowanie metody wahadłowej pracy wózków w wybranej strefie magazynu w celu minimalizacji strat w postaci oczekiwania i tzw. „multihandlingu” palet
- drobne zmiany konstrukcyjne wózków do kompletacji w celu poprawy ergonomii pracy
Efekty:
Implementacja wymienionych wyżej inicjatyw oczywiście wymagała szczegółowego zaplanowania i rozłożenia w czasie tak, aby wprowadzane zmiany w jak najmniejszym stopniu zagrażały płynności przebiegu procesów produkcyjnych. Po kilku tygodniach wzmożonych działań, wdrożenie zmian przez zespół projektowy pozwoliło m.in. na:
- ograniczenie zapotrzebowania na pracę w danym obszarze z 20 do 13 osób na zmianę(- 35%)
- jednoczesny wzrost średniej efektywności pracy magazynierów ze średnio 44% do docelowych 62% z dalszym potencjałem na długofalową optymalizację
- zmniejszenie realnej powierzchni magazynowej dedykowanej obsługiwanej części surowców o 5% i obniżenie wartości magazynu
- dodatkowe oszczędności w postaci ograniczenia wykorzystania wózków widłowych z docelowym potencjałem na redukcję floty
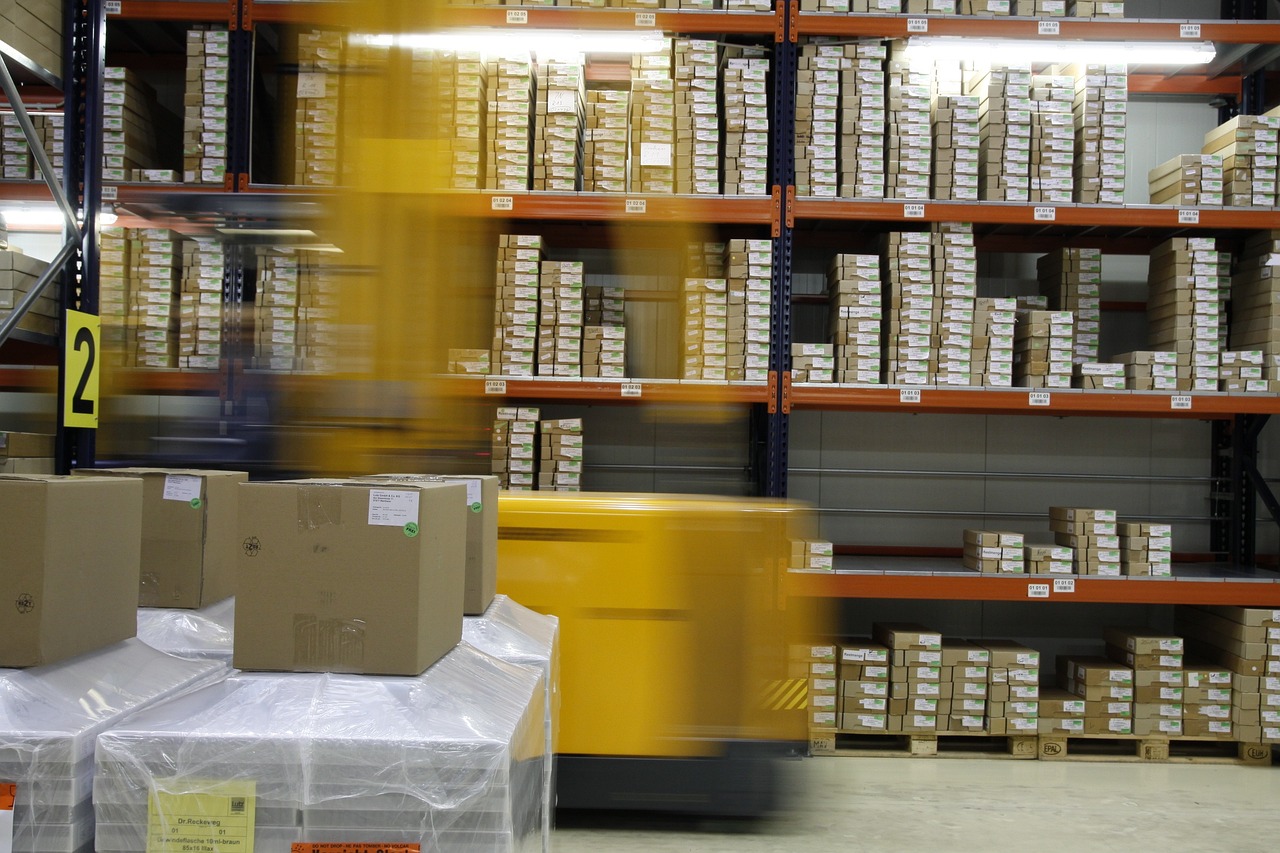
Podsumowanie
Konsekwentne trzymanie się podstaw zasad odchudzonej produkcji i metodyki problem solving (Raport A3 – PDCA) wraz z zastosowanie skutecznych narzędzie jakie niesie ze sobą metodyka normowania MTM, pozwoliła na skuteczne i szybkie wdrożenie zidentyfikowanych potencjałów. Co istotne dla klienta, działania w obszarze magazynu wpłynęły również na pozytywny trend obniżenia części pozycji kosztowych związanych m.in. z wartością magazynu surowca i docelowym obniżeniem kosztów operacyjnych obsługi wózków widłowych. Wdrożenie metodyki pracy podczas kompletacji pozwoliła poprawić średnią efektywności pracowników przy zachowaniu bezpiecznego balansu pracy. Na koniec, sama inwestycja w prace projektowe i wdrożeniowe pozwoliła na osiągnięcie realnego ROI z wprowadzonych zmian w okresie poniżej 12 miesięcy.
Życzymy wszystkim naszym klientom tak dużego zaangażowania w prace projektowe oraz chęci do wprowadzenia zmian w organizacji.
![]() | Marcin Żurawik Ekspert COO DB77 Consulting, Prezes Zarządu Pracuje w oparciu o autorską metodę pracy - ExeLean, której celem jest szybka i trafna diagnoza kluczowych obszarów każdej organizacji pordukcyjnej lub usługowej. Posiada doświadczenie w realizacji kilkudziesięciu projektów związancyh z szeroko pojętą optymalizacją procesów, w szczególności produkcyjnych. |
Technologie wspierające Lean
PARTNERZY SEKCJI:
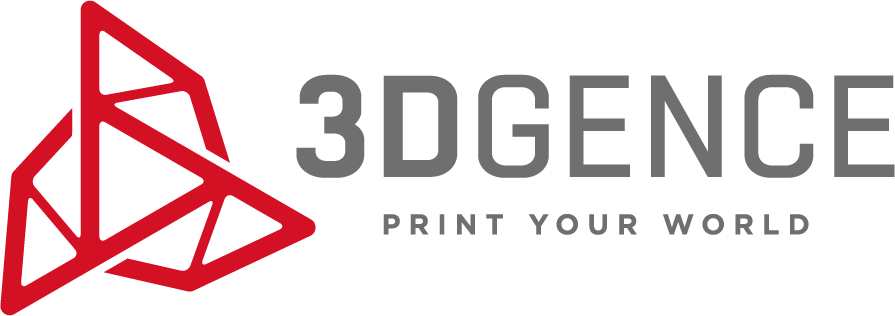
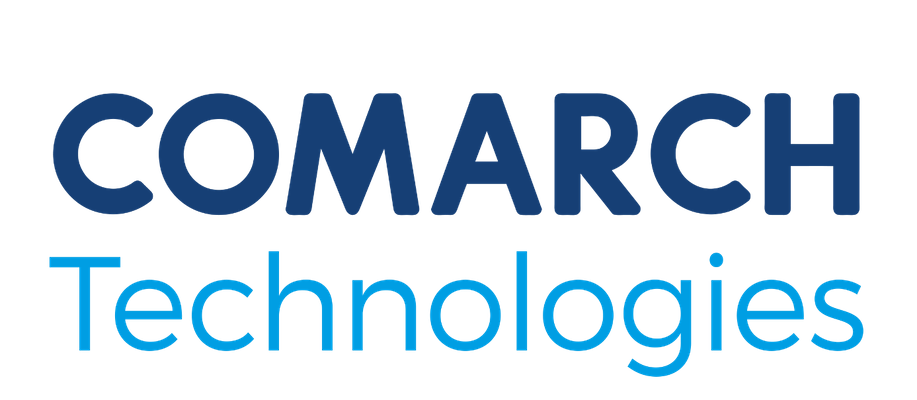
Śledź nas w social media
Aktualności
Zapowiedź: 17. Konferencji Lean | Six Sigma
Dobre praktyki Lean Higher Education
PolecamyZapraszamy serdecznie do udziału w 17. Konferencji Lean | Six Sigma, organizowanej przez Akademię Białego Kruka, która odbędzie się 6-7 czerwca we Wrocławiu. Wydarzenie stanowi wyjątkową okazję do spotkania oraz wymiany poglądów z czołowymi ekspertam ...
Dobre praktyki zarządcze, projektowe i narzędziowe – to temat przewodni tegorocznego XI seminarium LeanHE Poland. Wydarzenie organizowane przez Wydział Zarządzania i Ekonomii Politechniki Gdańskiej odbędzie się w dniach 24–25 czerwca.
Kalendarz konferencji Lean
Najbliższe szkolenia Lean
Patronujemy Wyszukiwarka
Śledź nas na Facebooku